Dry type transformers are a cornerstone of reliable and safe power distribution, offering significant advantages in various applications. However, like any critical electrical equipment, they require regular and proper maintenance to ensure continued optimal performance and a prolonged operational lifespan. Neglecting maintenance can lead to inefficiencies, unexpected failures, and costly downtime.
This blog delves into the essential aspects of dry type transformer maintenance, providing valuable insights and practical guidance. By understanding and implementing effective maintenance strategies, you can significantly extend the life of your transformer, safeguard your electrical systems, and ensure consistent and dependable power supply for your operations.
Dry Type Transformer Maintenance Checklist
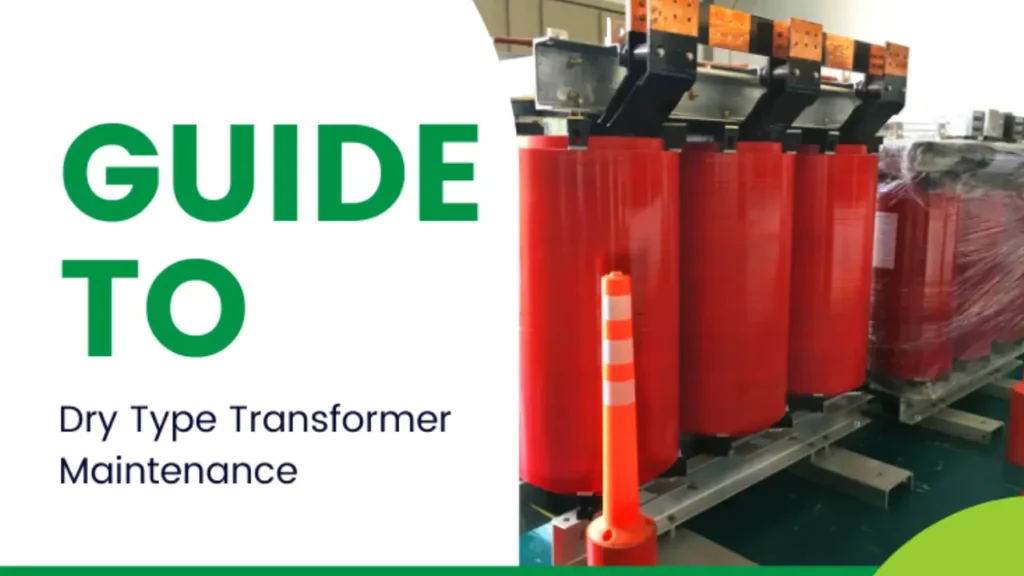
Dry-type transformers, known for their safety and environmental friendliness, require regular maintenance to ensure reliable operation and longevity. This checklist outlines key inspection points and procedures to keep your dry-type transformer in optimal condition.
Visual Inspection
A thorough visual inspection is the first line of defense in identifying potential issues. Carefully examine the transformer enclosure for any signs of damage, such as dents, rust, or paint deterioration. Check the ventilation openings to ensure they are free from obstructions like dust, debris, or foreign objects, which can impede proper cooling. Look for any evidence of oil leaks, although dry-type transformers do not contain oil as a primary insulation or cooling medium; any fluid leakage could indicate a problem with auxiliary components.
Cleaning
Accumulated dust and dirt on the transformer windings and core can act as thermal insulation, hindering heat dissipation and potentially leading to overheating. Regularly clean the transformer using a vacuum cleaner or compressed air to remove any buildup. Pay close attention to the ventilation ducts and cooling fins to ensure unobstructed airflow. Avoid using liquids for cleaning unless specifically recommended by the manufacturer and ensure the transformer is de-energized before cleaning.
Terminal Connections
Loose or corroded terminal connections can cause increased resistance, leading to overheating and potential failure. Inspect all electrical connections, including primary and secondary terminals, ground connections, and control wiring. Ensure all connections are tight and free from corrosion. If any signs of corrosion are present, clean the affected areas and re-tighten the connections. Periodic torque checks of bolted connections are also recommended according to the manufacturer’s specifications.
Insulation Testing
Insulation testing is crucial for assessing the health of the transformer’s insulation system. Perform insulation resistance tests (megger tests) on the windings to ground and between windings to identify any signs of insulation degradation or moisture ingress. Compare the test results with previous readings and the manufacturer’s recommendations. Polarization index (PI) and dielectric absorption ratio (DAR) tests can provide further insights into the condition of the insulation.
Temperature Monitoring
Monitoring the operating temperature of the transformer is essential for preventing overheating. Check the temperature of the windings and core using a temperature probe or infrared thermometer, especially under full load conditions. Compare the measured temperatures with the transformer’s temperature rating and previous readings. Investigate any significant temperature increases, as they may indicate overloading, inadequate ventilation, or internal faults.
Audible Noise and Vibration
Unusual noises or excessive vibrations can indicate underlying problems within the transformer. Listen for any humming, buzzing, or crackling sounds that deviate from the normal operating noise. Check for loose parts or components that may be causing vibrations. Investigate and address any abnormal sounds or vibrations promptly to prevent further damage.
Bushings and Insulators
Inspect the bushings and insulators for any signs of cracks, chips, tracking, or contamination. Clean any accumulated dust or dirt from their surfaces. Ensure that the connections to the bushings are tight and secure. Damaged or contaminated bushings can lead to flashovers and transformer failure.
Cooling System (if applicable)
While most dry-type transformers rely on natural air cooling, some larger units may have forced air cooling systems with fans. If your transformer has fans, ensure they are operating correctly and that the airflow is not obstructed. Check the fan motors for any unusual noises or vibrations and perform regular maintenance as recommended by the fan manufacturer.
Tap Changer (if applicable)
If your transformer is equipped with a tap changer, inspect it for proper operation. Ensure that the tap changer moves smoothly through its positions and that the contacts are clean and in good condition. Check the tap changer mechanism for any signs of wear or damage.
Documentation
Maintain accurate records of all maintenance activities, including inspection dates, findings, test results, and any repairs performed. This documentation provides a valuable history of the transformer’s condition and helps in identifying trends and planning future maintenance. Refer to the manufacturer’s recommendations and relevant industry standards for specific maintenance intervals and procedures.
Maintenance While the Dry Type Transformer is DE-Energized
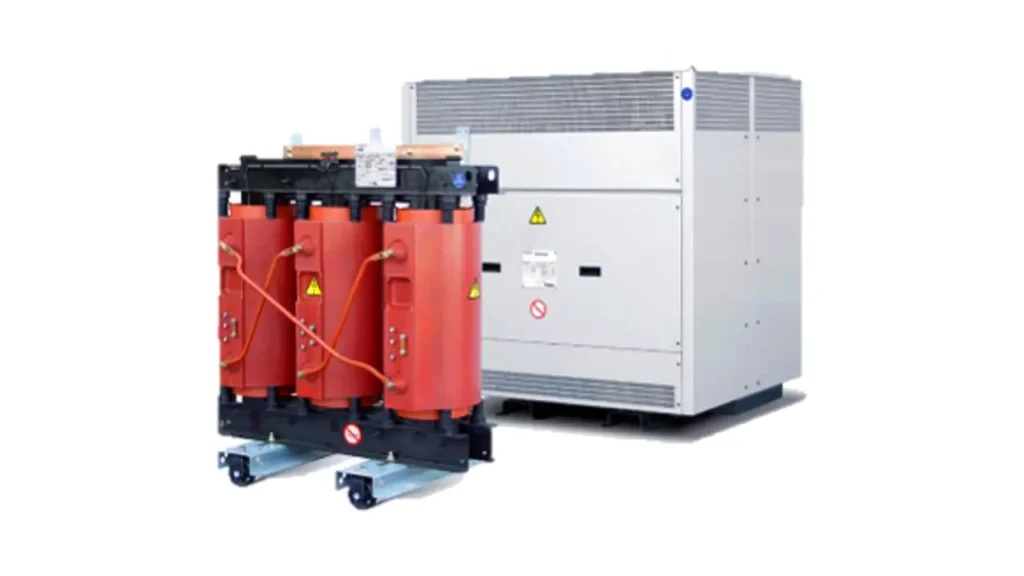
When the dry-type transformer is de-energized, it presents a crucial window for in-depth maintenance and inspection tasks that cannot be safely performed during operation. This downtime allows for meticulous examination of internal components and ensures the integrity of the entire system. By addressing potential issues proactively during this period, you can significantly reduce the risk of unexpected failures and extend the lifespan of your transformer.
During de-energized maintenance, focus on tasks such as thorough cleaning of windings and core to remove accumulated dust and debris that can impede cooling. Carefully inspect all terminal connections for tightness and signs of corrosion, ensuring secure electrical pathways. Insulation testing, including megger and polarization index tests, provides valuable insights into the health of the insulation system.
Additionally, a detailed visual inspection for any signs of physical damage, such as cracks or loose components, can be conducted safely. These comprehensive checks during the de-energized state are vital for maintaining the long-term reliability and safety of the dry-type transformer.
How to Check if Dry Type Transformer Needs to Be Repaired
Identifying whether a dry-type transformer requires repair involves a combination of keen observation during operation and systematic inspections during maintenance shutdowns. Subtle changes in its behavior or physical condition can be early indicators of underlying issues.
This guide outlines key signs and checks to help you determine if your dry-type transformer needs professional attention to ensure continued safe and reliable performance.
Unusual Noises
Pay close attention to the sounds emanating from the dry-type transformer during operation. While a low-level hum is normal due to magnetostriction, any significant increase in volume, or the appearance of new sounds like buzzing, crackling, or grinding, can indicate a problem.
These noises might be a sign of loose windings, core vibrations due to loose clamping, partial discharge within the insulation, or issues with the cooling fans if the transformer is equipped with them. Investigating unusual noises promptly can help identify and address minor issues before they escalate into major failures.
Excessive Vibration
A certain amount of vibration is expected from an energized transformer. However, if you notice a significant increase in vibration levels, or if the transformer begins to shake noticeably, it could signal a developing fault. Increased vibration can be caused by loose core clamps, winding movement due to electromagnetic forces, or even degradation of the anti-vibration pads beneath the transformer. Ignoring excessive vibration can lead to accelerated wear and tear on the transformer’s components, potentially causing more severe damage over time.
Discoloration or Overheating
Visual inspection of the transformer’s windings and insulation can provide clues about its operating condition. Look for any signs of discoloration, such as darkening or charring of the insulation material. These changes often indicate that the transformer has been subjected to excessive heat, potentially due to overloading, poor ventilation, or internal faults. Additionally, if the transformer enclosure feels excessively hot to the touch during normal operation, it’s a strong indicator of an overheating issue that needs investigation. Persistent overheating can lead to premature insulation failure and significantly shorten the transformer’s lifespan.
Failed Insulation Tests
Regular insulation resistance tests, such as megger tests, are crucial for assessing the health of the transformer’s insulation system. A significant drop in insulation resistance compared to previous readings or manufacturer specifications indicates a degradation of the insulation. Similarly, abnormal results from Polarization Index (PI) or Dielectric Absorption Ratio (DAR) tests can also point towards insulation problems, potentially caused by moisture ingress, contamination, or thermal aging. Failed insulation tests are a clear sign that the transformer’s ability to safely contain electrical current is compromised and that repair or replacement may be necessary.
Visible Damage
A thorough visual inspection of the transformer enclosure, bushings, and connections should be part of routine maintenance. Look for any signs of physical damage, such as cracks, dents, or deformation of the enclosure. Inspect the bushings for chips, cracks, or tracking marks. Check all electrical connections for looseness, corrosion, or signs of overheating. Any visible damage could compromise the transformer’s structural integrity, insulation, or electrical connections, necessitating repair to ensure safe and reliable operation.
Oil Leaks (if applicable to auxiliary components)
While dry-type transformers do not use oil as their primary insulation or cooling medium, they may have auxiliary components like tap changers or some types of cooling systems that contain oil. Inspect these components for any signs of oil leaks. Leaks can indicate seal failures or damage to the component itself, potentially leading to operational issues with the auxiliary system and requiring repair.
Tests to Conduct for Routine Dry Try Transformer Maintenance
Routine maintenance of dry-type transformers involves a series of tests designed to assess their operational health and identify potential issues before they lead to failures. These tests provide valuable data on the condition of the insulation, windings, and overall integrity of the transformer. Regular testing ensures safety, reliability, and extends the lifespan of the equipment.
Insulation Resistance Test (Megger Test)
The insulation resistance test, commonly performed using a megohmmeter (megger), measures the resistance between the transformer windings and ground, as well as between the windings themselves. This test helps to evaluate the condition of the insulation material. Low insulation resistance readings indicate potential insulation degradation due to moisture, contamination, or thermal aging. Tracking insulation resistance values over time can reveal trends and help predict potential insulation failures.
Polarization Index (PI) Test
The Polarization Index (PI) test is an extension of the insulation resistance test. It involves taking insulation resistance readings at two different time intervals, typically at 1 minute and 10 minutes, and then calculating the ratio of the 10-minute reading to the 1-minute reading. The PI value provides further insight into the condition of the insulation. A low PI value (typically less than 2) suggests that the insulation may be contaminated or have absorbed moisture, indicating a need for further investigation and potential remedial action.
Dielectric Absorption Ratio (DAR) Test
Similar to the PI test, the Dielectric Absorption Ratio (DAR) test also assesses the quality of the insulation. It involves taking insulation resistance readings at shorter time intervals, such as 30 seconds and 60 seconds, and calculating their ratio (60-second reading divided by the 30-second reading). The DAR value reflects the insulation’s ability to absorb charge over time. A low DAR value can indicate insulation problems similar to those identified by a low PI value.
Winding Resistance Test
The winding resistance test measures the DC resistance of the transformer windings. This test helps to identify issues such as loose connections, broken strands in the windings, or high resistance joints. Abnormally high resistance in a winding can lead to increased losses and overheating. Comparing the measured resistance values with the manufacturer’s specifications and previous readings can reveal any developing problems within the windings.
Turns Ratio Test
The turns ratio test verifies the ratio of the number of turns in the primary winding to the number of turns in the secondary winding. This test ensures that the transformer will provide the correct output voltage for a given input voltage. An incorrect turns ratio can indicate shorted turns within a winding or other internal faults. This test is typically performed using a turns ratio meter.
Excitation Current Test
The excitation current test measures the current drawn by the primary winding when the secondary winding is open-circuited and the rated voltage is applied to the primary. An abnormally high excitation current can indicate problems with the magnetic core, such as shorted laminations, air gaps, or faults in the windings. Comparing the measured excitation current with previous readings and the manufacturer’s data can help identify core-related issues.
Impedance Test (Short-Circuit Test)
The impedance test, also known as the short-circuit test, determines the equivalent impedance of the transformer. This test is usually performed by short-circuiting one winding (typically the low-voltage side) and applying a reduced voltage to the other winding until rated current flows. The impedance test helps to identify winding deformations or other structural changes within the transformer that might have occurred due to short circuits or mechanical stresses.
Temperature Monitoring
While not a direct electrical test, regular temperature monitoring using temperature probes or infrared thermometers is crucial for routine maintenance. Monitoring the temperature of the windings and core under various load conditions helps to ensure that the transformer is operating within its thermal limits. Significant deviations from normal operating temperatures can indicate overloading, cooling system issues (if applicable), or internal faults.
Conclusion
In conclusion, proactive and consistent dry type transformer maintenance is paramount for maximizing their operational lifespan and ensuring the safety and reliability of your power distribution system. Regular inspections, cleaning, and timely repairs can prevent minor issues from escalating into costly failures, safeguarding your investment and minimizing downtime. By adhering to a well-structured maintenance plan, you can significantly extend the service life of your transformers.
For businesses seeking to establish or expand their power infrastructure with dependable components, sourcing from reputable suppliers is crucial. Linkwell Electrics offers a potential avenue for acquiring wholesale dry type transformers, emphasizing the importance of quality and durability for long-term performance. Investing in robust transformers and a comprehensive maintenance strategy go hand in hand.
Ultimately, understanding and implementing effective dry type transformer maintenance practices is a smart and cost-effective approach to ensuring a stable and efficient power supply. Partnering with reliable suppliers like Linkwell Electrics for your transformer needs further supports the longevity and performance of your electrical systems, contributing to operational continuity and reduced long-term expenses.