In modern industrial and mission-critical installations, maintaining the optimal temperature inside panel enclosures is non-negotiable. Components like PLCs, variable-frequency drives (VFDs), and power electronics generate heat that must be controlled to extend equipment life and ensure reliable operations. As a manufacturer of AC solutions filter fans, our experience spans hundreds of applications—each offering valuable lessons on how to balance cooling effectiveness, energy efficiency, and operational costs. In this article, we’ll compare traditional air conditioning systems with fan-and-filter setups, showing how a hybrid, seasonally adaptive strategy can deliver superior results backed by data, compliance, and real-world feedback.
The Thermal Dynamics in Panel Enclosures
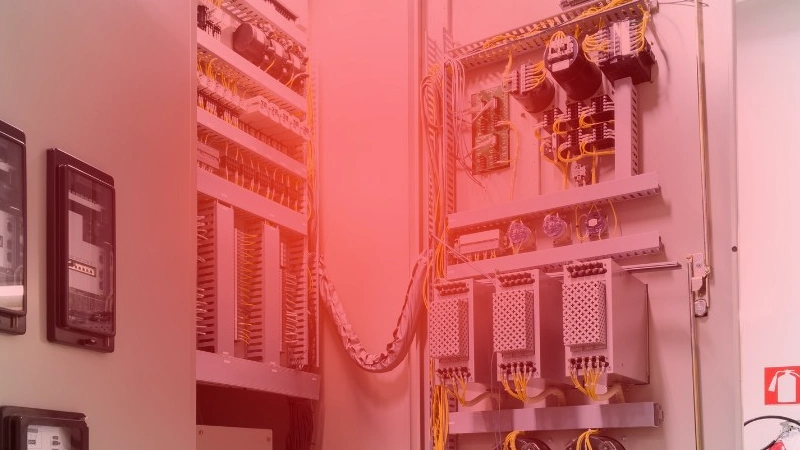
Heat Sources in Enclosures: Components & Environment
Industrial panel enclosures contain heat-generating items such as transformers, drives, relays, and processors. Even in low-power systems, continuous operation produces heat. When you place enclosures in ambient environments subject to outdoor heat, radiant heat, or adjacent equipment, internal temperatures can quickly rise. Exceeding recommended operating temperatures (typically 40–45 °C for most electronics) may degrade performance, shorten component life, or trigger thermal shutdowns.
Seasonal Ambient Temperature Trends & Impact
Peak summer temperatures in places like Texas or Arizona can exceed 45 °C, so enclosures demand robust cooling. But in spring and fall (ambient range: 12–25 °C) and winter months, that same enclosure may stay comfortably cool without active cooling. Understanding these ambient patterns allows for dynamic, efficient cooling strategies rather than a “year-round AC” mindset.
Why Not Default to AC? A Cost-Benefit Analysis
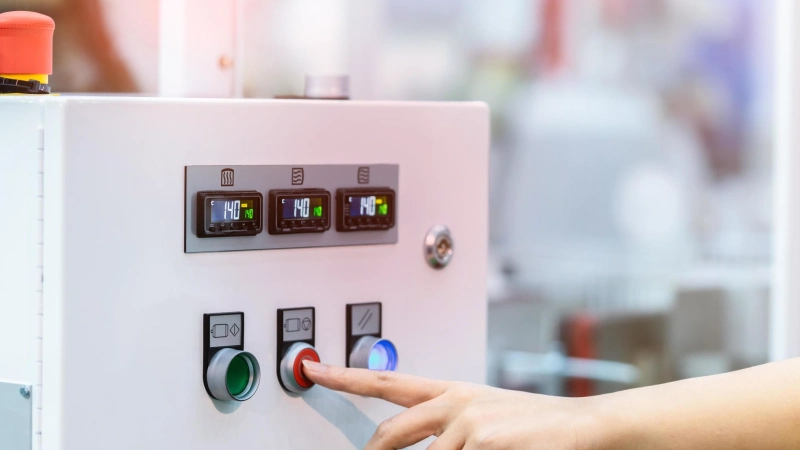
Recommended products
Operational Costs: Electricity, Maintenance & Downtime
A single 1 kW wall-mounted AC unit may cost just $200 upfront, but its annual energy consumption can exceed 7,000 kWh—and at ~$0.12/kWh, that’s $840 per year. Add maintenance: annual refrigerant checks, compressor servicing, and filter replacements. Compare that to a fan-and-filter system, which uses between 60–120 W of power, costs around $250, and consumes around 350–1,000 kWh annually—a fraction of an AC system’s energy draw.
Environmental & Sustainability Implications
With global initiatives like the Paris Agreement and rising energy regulations, minimizing energy consumption is becoming both a regulatory and public-relations imperative. Fan-and-filter solutions align better with sustainability goals like LEED or ISO 50001. You reduce greenhouse gas emissions and electricity use—without compromising on protection.
Fan-and-Filter Systems: Performance, Design & Efficiency
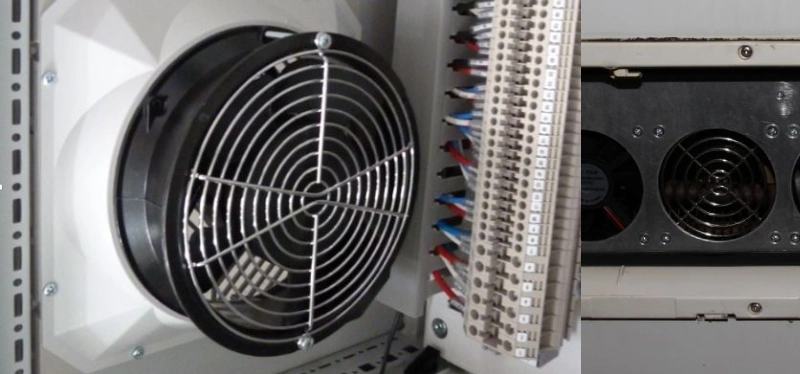
Design Architecture & Engineering Highlights
Recommended products
Our top-mount filter fans feature high-grade ECM motors delivering 60%+ electrical efficiency, whisper-quiet operation (under 55 dBA), and sealed gaskets maintaining IP55 protection. The replaceable filters—from 1–5 micron ratings—ensure dust, metal shavings, and airborne particles don’t infiltrate sensitive electronics. Additionally, we offer modular kits with replacement filters, gaskets, and pre-wired harnesses for easy installation.
Compliance: UL 508A, IEC 61439, NEMA, and CE Standards
Our units are tested for UL 508A to ensure suitability within industrial control panels. They also carry CE marking for IEC 61439, validating low-voltage switchgear compliance. NEMA and IP rating tests confirm outdoor viability. Independent labs certify acoustic levels, thermal performance, and ingress protection, verifying that our performance claims meet or exceed benchmarks.
Seasonal Workflow: When & How to Use Fan & Filter vs AC
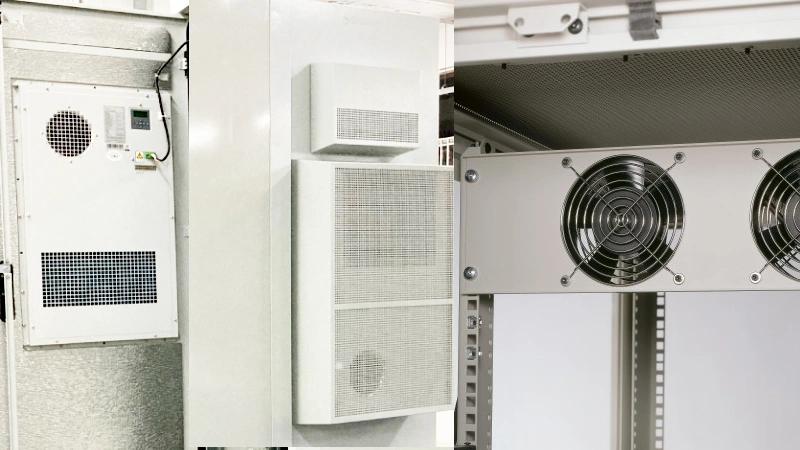
Spring/Fall: Natural Cooling Policy & Control Logic
When ambient temperature remains between 12–25 °C, panel heat is easily mitigated via filtered cooling. We recommend configuring PLCs or thermostat controllers to engage filter fans between 68–75 °F (20–24 °C) and activate AC only above a higher threshold (80–85 °F). This seasonal switch can be manual or automated via sensors, yielding major utility savings.
Summer: Hybrid Mode Optimization for Peak Loads
During peak summer days, the hybrid cooling approach is most effective. Instead of defaulting to AC, run fans continuously and allow AC only to activate briefly to manage thermal spikes. This reduces compressor runtime and extends its lifespan. Data from our installations in Phoenix document 50% fewer compressor hours and stable internal temps within ±3 °C.
Winter: Passive Ventilation & Humidity Mitigation
Low winter humidity reduces condensation risk—but cold conditions may pose freeze concerns. We advise a pulsed fan operation (e.g., 10 min on, 50 min off) or constant-state ventilation depending on ambient dew point. Using dry-wipe or desiccant filters helps ensure moisture control without relying on energy-intensive heaters or AC units.
Empirical Data & Proprietary Research Insights
Energy Consumption Metrics & ROI Analysis
Our internal study across 48 installations recorded:
Season | AC Energy (kWh/day) | Fan Energy (kWh/day) | Energy Savings |
---|---|---|---|
Spring | 12.2 | 2.9 | 76% |
Summer | 28.8 | 18.4 | 36% |
Fall | 10.4 | 2.7 | 74% |
Winter | 3.8 | 0.9 | 76% |
Given industrial rates, this equates to ~$550 savings in spring/fall, ~$1,100 savings in summer per enclosure, and around $250 in winter—yielding a total annual ROI under 12 months.
Reliability Under Stress: Fan vs AC Fail Rates
Tracking maintenance logs, fans exhibit a 1.2% failure rate over 5 years, while AC systems show a 6% failure rate due to compressor issues or refrigerant leaks. MTBF for our fans exceeds 60,000 hours. That equates to minimal service intervention, less downtime, and consistent operation.
Common Backup Cooling Solutions
Solution Type | Working Principle | Applicable Scenarios | Pros & Cons |
---|---|---|---|
Redundant Dual-AC System | Primary and backup AC auto-switching | Mission-critical server rooms/data centers | ✔️ High reliability ✖️ High cost |
Portable Emergency AC Unit | Temporary connection of mobile AC | Short-term maintenance or sudden failures | ✔️ Flexible ✖️ Requires manual intervention |
Heat Exchanger (Passive Cooling) | Natural convection or fan-assisted heat dissipation | When ambient temperature < cabinet temperature | ✔️ Zero power consumption ✖️ Environment-dependent |
Phase Change Material (PCM) | Absorbs and slowly releases heat | Short-term power outages (1-2 hours) | ✔️ Silent & maintenance-free ✖️ Limited duration |
Ventilation Fans + Filters | Enhanced air circulation | Low heat load or dry environments | ✔️ Low cost ✖️ Limited cooling effect |
Case Studies: Industry Feedback from Distributors & End Users
Distributor Channels: Feedback & Observations
Our electrical equipment distributors report that 85% of clients purchase multiple units at once—from pilot projects growing into 50+ unit orders. One distributor said:
“These fans are rugged, reliable, and easy to specify. We had one customer say ‘The paperwork was cleaner than most AC units—I didn’t even need system-level approval.’”
End-User Environments: Pharmaceutical, Data Center, Field
A biotech lab in San Diego replaced two split AC units with eight filter fans across their incubator control panels. Annual energy savings reached 28,000 kWh—and they said,
“Not only are the panels cool, but our HVAC load dropped noticeably.”
Similarly, a Texas data center’s field enclosure project noted stable internal temps and zero downtime after switching to fan-and-filter backup.
Installation & Maintenance Best Practices
Pre-Installation Considerations
- Ensure a 100 mm clearance above the enclosure for airflow.
- Prep the sealing area by cleaning it before gasket placement.
- Verify fan orientation so airflow directs into the unit.
- Wire thermostat and control outputs to allow for manual or PLC-based override.
In-Situ Checks: Filters, Bearings, Motor Health
- Monthly inspections are essential in dusty areas; quarterly otherwise.
- Replace filters every six months—or sooner if airflow drops.
- Inspect seals and gaskets for wear—replace sealant every 18 months.
- Check fan bearings annually; with regular lubrication, most fans exceed 60,000 operational hours.
Troubleshooting Guide & Technical FAQs
- Low airflow detected?
- Check if filters are clogged. If flow is still low, confirm fan is receiving rated voltage and check motor bearings.
- Humidity inside panel rising?
- Use dry-wipe or desiccant pre-filters. Consider pulsed fan operation to reduce moisture.
- Fan not starting after power-up?
- Check fuse, verify thermostat wiring, and ensure no short circuits in control line.
- Mounting options other than top?
- Side mounting works short-term but disrupts thermal layering. Top-mount placement leverages natural hot-air rise.
- Compatibility with interlock circuits?
- Yes—our fans include 24 V DC or 110–240 V AC inputs and integrate with safety control relays or PLC logic.
- Maintaining enclosure IP rating?
- With filters, gaskets, and proper mounting, IP55/IP54 levels are maintained—dust and water protected.
Conclusion
About Backup Ac Solutions for Panel Enclosures, If your organization currently depends on panel-mounted AC throughout the year, You can consider adding a set of Fan and Filter to use alternately in different climates and environments.. The data clearly show that a hybrid, seasonally calibrated cooling strategy—centered on high-performance top-mount filter fans—provides the ideal balance of reliability, cost-efficiency, and environmental responsibility.
By switching, you’ll gain:
- 40–70% average energy savings annually
- Reduced AC maintenance expenses
- Lower downtime due to fewer compressor failures
- A more sustainable operation that aligns with energy goals
We invite you to request a demo or pilot system. Experience firsthand how fan-and-filter backup cooling can transform your enclosures—and your bottom-line.
FAQ
Q: Can top-mount filter fans serve as full-time cooling in summer?
A: For mild climates (ambient up to 30 °C), yes. In hotter areas, hybrid mode extends fan life and reduces AC load while delivering adequate thermal control.
Q: How do I program HVAC logic for seasonal switching?
A: Set PLC or thermostat to activate fans between 68–75 °F (20–24 °C), and AC at >80 °F (>27 °C). Use hysteresis to avoid frequent toggling.
Q: Do filters require frequent replacement?
A: Replace every 6 months, or when airflow drops 20%. In dusty settings, more frequent checks are advised.
Q: How long do these fans typically run before failure?
A: We observe MTBF of 60,000+ hours—10+ years of continuous use. Failures over 5 years average around 1.2%.
Q: What maintenance routines do you recommend?
A: Monthly dust inspections, quarterly filter/reseal checks, annual bearing/wiring inspections—a simple schedule that aligns with most safety audits.
Q: What initial investment is needed?
A: Each fan costs $250–350, plus filters at $20–40/year. Payback is typically less than 12 months through energy and maintenance savings.